Steps To Creating Products Through Investment Casting
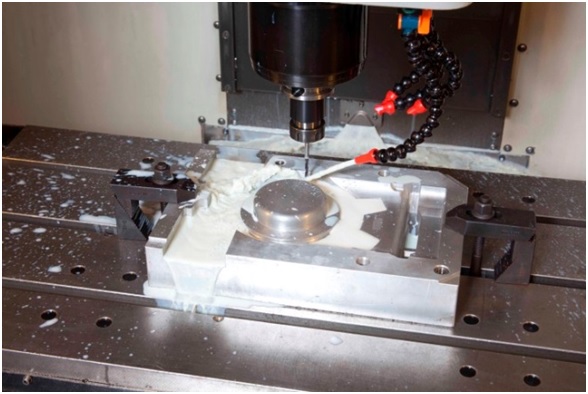
Investment casting is a method to form metal with parts having precise dimensions with tight tolerances. This method has existed for years although methodology and innovations in equipment have allowed keeping pace with today’s demand. It is a great idea to consider investment casting over other options for the ability to work with various materials and saving time. Read on to get insights into the steps to create products through investment casting.
Creating the wax-injection tooling
Wax patterns were created from beeswax in ancient times by hand and making one by one. However, creating a wax pattern for every cast today is done by using wax-injection dies. The tooling is a permanent item for every component. This is replaced when damaged or there’s a need to change the design. Aluminum is the primary material for making dies manufactured through CNC machining.
The die shape corresponds to the final product’s negative relief with allowance for wax and material for final casting to shrink. The injection process requires the use of non-abrasive wax for dies with the potential to produce endless shots without too much maintenance with limited chances of damage or replacement.
Producing wax patterns
The next step is to set the pattern wax temperature enough to make it semi-liquid or with a paste consistency. While in this state, wax is injected into a die to form a pattern slightly larger compared to the final casting created because of shrinkage. This injection is repeated multiple times to produce the desired number of patterns to match order requirements. During the process of investment casting coating, the wax composition varies.
Assembling wax patterns
The next step is to form a tree by combing multiple wax patterns on a similar sprue. This significantly enhances investment casting efficiency. The assemblies support various patterns to undergo the remaining steps together instead of casting a single part. After producing a given number of wax patterns, these are fixed to wax bars forming a tree or cluster.
Afterward, the patterns are placed where the gates are positioned or where the metal enters after individual casting. Adequate size is necessary for the tree to offer enough feed metal for providing sound casting while metal solidification takes place. The price of the final casting depends on how many patterns are assembled when forming the tree. A tree with lower patterns costs significantly lower.
Creating the Investment Shell
The next step is dipping the assembled trees in refractory slurries before coating using various types and sizes of stucco. This produces a ceramic shell surrounding the wax. Wax has exposed one end while coating to ease removal in the phase. The initial coat is important for producing a quality surface finish. It involves applying slurry by dipping in the wax tree before covering it with zircon sand and left to dry. Additionally, slurry is added before coating with coarse silica sands to enhance mold strength.
Dewaxing the mold
With the ceramic mold now fully coated, it is time to remove the wax before filling the mold with metal. Completing the task involves placing an autoclave with the end exposed to wax facing down. The autoclave is shut before injecting steam in seconds to pressurize the vessel and expose the mold to extreme temperature. The molten wax drains out at the mold end for reuse. After some time, the mold is removed to cool and dry from the autoclave.
Pre-heating the mold
After removing wax from the mold, it is still not ready for filling with molten metal. The ceramic mold requires firing at an adequate temperature before filling with the hot metal. Curing the ceramic mold requires heating at 1,900 degrees F. The firing also burns out any remaining wax in the mold to prevent casting defects. Other benefits of firing the ceramic mold include:
- Boosting the mold strength
- Allowing simultaneous shrinking of mold and cast to enhance dimensional accuracy
- Allowing molten metal to keep its liquidity throughout the mold
Pouring the casting
After firing the ceramic mold, metal is poured for melting to prepare for poring. Melting the metal requires an induction furnace relying on electricity and magnetism for heat generation. This allows quick liquefaction of the metal ingot at about 3,000 degrees F before getting out of the oven for pouring. Metal enters the mold cavity fast then the mold is left to cool for the metal inside to begin solidifying.
Cleaning the castings
With the casting now at room temperature, it is time for cleaning involving cleaning the ceramic mold and grinding the gates away. With the once-strong mold spent and shaken away using blasting and vibration. The individual casting is separated from the metallic tree with subsequent removal of the gates through grinding. Then, the casting is removed and sandblasted to eliminate the remaining ceramic as well as enhancing the product’s surface finish before the inspection.
Completing the casting
Finally, heat treatment is applied to enhance the product’s physical properties. Afterward, the sandblasting of the casting happens before the final inspection. The good thing about investing in casting is producing net shape or near-net shape products with dimensional precision without additional machining.
Conclusion
Investment casting is a wonderful manufacturing process that allows producing castings with exceptional precision. This significantly lowers costs and saves time while working with various materials.