Four Essential Things To Know About Surface-Mount Technology
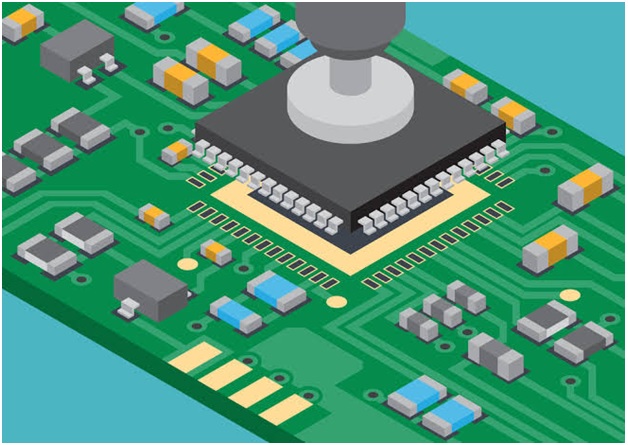
Electronics manufacturing uses surface-mount technology (SMT) to mount individual components to a printed circuit board. Traditionally, through-hole technology (THT) was used extensively to put together PCBs. But in recent years, SMT is gaining more popularity because of the convenience in budget and time that this technique provides. In THT, the leads of individual components pass through the PCB. The leads are then soldered onto pads or land on the underside of the board through the wave soldering process. But with the advent of SMT, the placing of components takes place ten times faster than THT components. SMT provides better stability, reliability, and efficiency in the soldering process.
Using SMT technology, any component that you mount on a PCB is known as a surface-mounted device. SMT has revolutionized the PCB industry. You can easily solder the components using SMT framed stencil on the circuit board. The stencils generally consist of a bare stainless steel sheet with defined openings to efficiently deposit solder paste to the board and attach the SMD to board pads. These stencils are precision tools for SMD placement.
Types Of SMT Soldering Process
The two main methods for SMT soldering include:
- Wave Soldering: Wave soldering is a large-scale soldering process to solder electrical components on a PCB. It entails a small bath of molten solder, which flows out to create a small wave. You need to pass the board and components over the wave for soldering.
- Reflow Soldering:It is more widely used than wave soldering in PCB assembly. Apply the solder on the board through a solder screen. Place the components on the board and hold it through solder paste. Pass the board through an infra-red heater that melts the solder to form strong joints with excellent electrical conductivity and mechanical strength.
How Does SMT Electronics Assembly Work?
The SMT electronics assembly includes the following production steps.
- Apply Solder Paste: It is the primary step in the SMT assembly process. You need to “print” solder paste on the circuit board via a silk-screen method. Based on the board design, use a stencil with the correct aperture and thickness to “print” the paste onto the board. Use the suitable product-specific paste. A custom-built laser-cut stainless-steel stencil custom provides better accuracy and efficiency in the printing process. Apply the soldering paste to areas where you need to solder the SMDs. Once you release the solder paste, subject it to 2D-soldering paste inspection to gauge to check if it is correct and even. Then transfer the board to the SMT assembly line for soldering of components.
- Component Placement and Assembly: Load the components for assembly in an SMT machine. Use intelligent software systems to prevent components switching or misloading. The SMT assembly machine uses a vacuum pipette to automatically removes each component and place it accurately on the board. Once the SMT assembly is complete, you need to move the boards to Reflow ovens for soldering.
- Component Soldering:The Reflow-soldering process subjects the board to a nitrogen atmosphere. The air is gradually warmed up to melt the soldering paste and vaporize the flux to fuse the circuit board components. It would help if you cooled down the board then permanently fix the components to the board.
- AOI and Visual Check: AOI visual inspections are essential to identify any errors in the SMT production line. You should check the board’s appearance in detail to ensure that it meets the predefined image. It helps ensure the consistency and accuracy of the SMT circuit board.
Different SMT Components Categories
- Passive: Passive components generally consist of larger resistors or capacitors. The addition of metal areas on the SMD allows it to undergo soldering. These components help in regulating electrical power that flows through them, making them “passive” components.
- Transistors and Resistors: These SMDs are relatively more minor in size. They are semiconductor electronic devices that facilitate the regulation of electrical power and electronic signals better than capacitors.
- Diodes: The use of diodes in SMDs enables the electric current to flow in a single direction in a circuit board. When you join a P-type and N-type semiconductor form an SMD, it functions similar to an intrinsic semiconductor.
- Integrated circuits: These are complex SMDs, and can get tricky to handle because of the multiple individual pins. It is produced as logic chips and other more advanced components.
Advantages Of Surface Mount Technology
Since you do not have to drill the circuit board for assembly, the SMT process is faster for production as compared to through-hole technology. It leads to lower initial costs. You can place the components closer together on the circuit board through SMT assembly. Hence, it helps to create smaller PCB designs. The solder joints are more stable and provide better mechanical performance under different conditions. PCBs produced with the SMT process are more compact and have higher circuit speeds. You can place components on both sides of the circuit board and in higher density.
To Conclude:
These points will give you an overview of the SMT assembly in PCB fabrication and assembly. It will enable you to create robust PCB designs, cut down production costs, and release high-quality boards in the market faster.