Ek Rupee Coin Ka Manufacturing Cost Kitna Hoga?
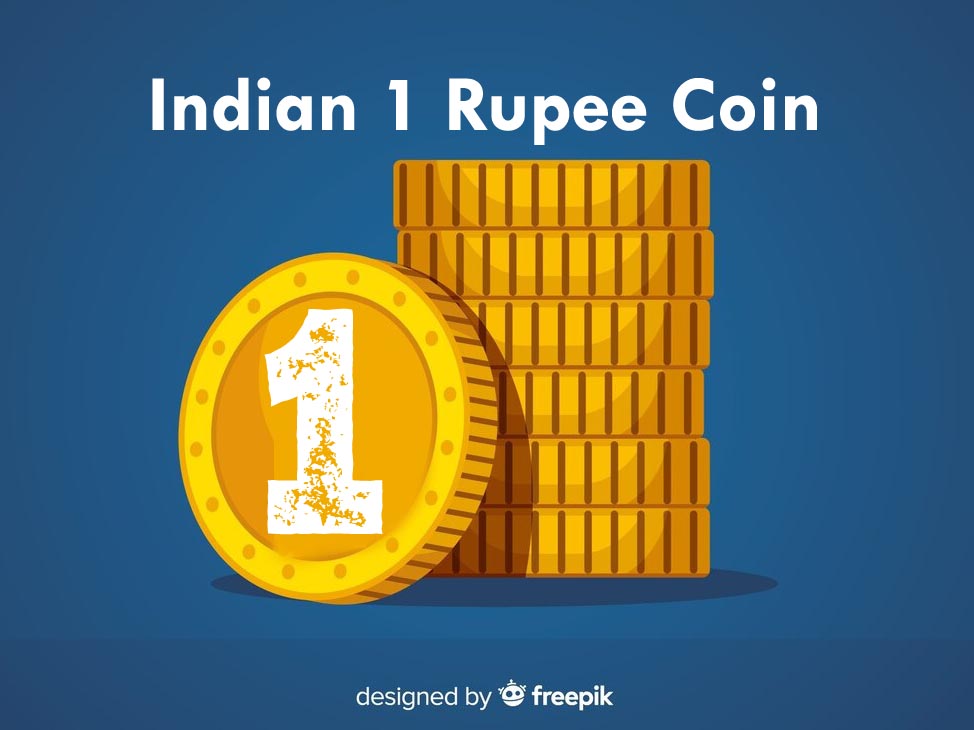
Freepik.com
Ek Rupee Coin Ka Manufacturing Cost Kitna Hoga? (Hindi)
Bohat say log sawal karte hain k ek rupee coin ka manufacturing cost kitna hoga? India mein, ek rupee ke sikke ki manufacturing cost actual value se zyada hoti hai. Estimate ke mutabiq, ek rupee ke sikke ko banane ki cost lagbhag 2 se 3 rupee ho sakti hai. Ye sarkari data aur minting ka process dekh kar vary kar sakti hai. Ye cost zyada hone ka ek bada reason hai ki government ko quality aur durability ka dhyan rakhna padta hai, taki sikka lambe samay tak chale aur asaan se kharab na ho.
Ek Rupee Coin Ka Manufacturing Cost Kitna Hoga: Dependent On Factors
Indian 1-rupee coin, Ek rupee ke sikke ki manufacturing cost kaafi factors par depend karti hai, jaise ki:
- Material ka cost: Ek rupee ke sikke mein aam tor par stainless steel ya nickel-brass ka use hota hai. Is material ki cost market ke rate ke mutabiq hoti hai.
- Minting Process: Sikke ko banane ke liye jo machinery, electricity aur labor lagti hai, woh bhi manufacturing cost mein shamil hoti hai.
- Transportation aur Distribution: Sikke ko mint se banks tak le jaane ki cost bhi add hoti hai.
1 Rupee Coin Making Cost
The 1 Rupee Coin Making Cost in India is a multifaceted aspect of the nation’s minting process, intricately tied to both material and operational expenditures. Each coin, crafted predominantly from stainless steel or nickel-brass alloys, incurs a production cost that encompasses raw materials, labor wages, and overhead expenses related to the manufacturing facilities. The intricate designs on the 1 Rupee coin also require precision engineering and advanced minting technologies, further influencing its overall expenditure. Additionally, fluctuations in global metal prices can significantly impact the 1 Rupee Coin Making Cost, necessitating careful financial planning by the Reserve Bank of India to ensure that currency remains economically viable while retaining its functional integrity within everyday transactions. The strategic management of these costs not only affects fiscal policies but also reflects broader economic conditions within which this essential denomination operates.
Manufacturing Cost Of 1 Rupee Coin
The manufacturing cost of 1 rupee coin in India is a multifaceted consideration that encompasses various elements, including raw material expenses, labor costs, and operational overheads. Predominantly composed of metals such as nickel-brass or stainless steel, the initial procurement of these materials plays a crucial role in determining the overall expenditure associated with each coin’s production. Following this, skilled artisans and industrial workers contribute to the minting process through intricate procedures that involve designing, stamping, and quality assurance—each step demanding precision and care. Furthermore, logistical factors such as transportation and distribution add another layer to the financial equation. The Reserve Bank of India’s meticulous oversight ensures that all aspects are optimized for efficiency while maintaining the integrity of currency production. Consequently, understanding the manufacturing cost of 1 rupee coin not only highlights economic implications but also reflects broader themes regarding resource allocation within India’s vibrant economy.
Ek Rupee Coin Ka Manufacturing Cost Kitna Hoga?
The manufacturing cost of a 1 Rupee coin in India is estimated to be approximately ₹1.11, according to disclosures by the Reserve Bank of India (RBI) from 2018.
This Manufacturing Cost Of 1 Rupee Coin Includes:
- Raw Materials: Materials like stainless steel or aluminum-bronze alloys.
- Production Costs: Expenses for machinery, labor, and energy during minting.
- Operational Costs: Quality checks, packaging, and transportation to distribution centers.
It is notable that the manufacturing cost often exceeds the face value of the coin, as durability, precision, and circulation needs are prioritized in the minting process.
Ek Rupee Coin Ka Manufacturing Cost Kitna Hoga? Factors Affecting The Manufacturing Cost Of One Rupee
- Several factors influence the manufacturing cost of a one rupee coin. The type of material used is crucial. Each material, be it metal or polymer, has its own price fluctuations based on market demand.
- Labor costs also play a significant role. Skilled workers are needed for precise minting processes, and their wages can vary significantly depending on location and expertise.
- Additionally, energy prices impact production expenses. A rise in electricity rates directly affects the overall cost to produce coins.
- Logistics can’t be overlooked either. Transporting raw materials to manufacturing plants incurs costs that ultimately factor into each coin’s price.
- Government regulations and taxes may impose additional financial burdens that affect how much it costs to mint currency effectively. Each element contributes uniquely to the final tally behind every single one rupee coin produced.
How Many 1 Rupee Coins Equal 1 kg?
The weight of a 1 Rupee coin is approximately 3.76 grams. To determine how many coins make up 1 kilogram 1000 grams
Cost Of Making 1 Rupee Coin
The Cost Of Making 1 Rupee Coin in India involves a meticulous process that combines raw material expenses, labor, and technological investment. Each coin is composed primarily of stainless steel or nickel-brass alloy, materials selected for their durability and resistance to corrosion. The cost encompasses not only the procurement of these metals but also the intricate machinery required for minting, which includes high-precision stamping presses that ensure uniformity and quality control in each piece produced. Additionally, factors such as energy consumption during production and overhead costs associated with operational facilities contribute significantly to the overall expenditure. Labor costs play a crucial role as well; skilled workers are essential for maintaining the sophisticated equipment used in minting processes while ensuring adherence to stringent security protocols aimed at preventing counterfeiting. Thus, analyzing the Cost Of Making 1 Rupee Coin reveals a complex interplay of materials science, engineering precision, and economic strategy within India’s monetary framework.
Breakdown Of Costs Involved In Manufacturing One Rupee
The primary metal used in indian 1-rupee coin is a blend of nickel and copper. This alloy provides durability while maintaining cost-effectiveness. Next comes labor costs. Skilled workers handle the precise minting process, ensuring each coin meets quality standards. Machinery and technology play a crucial role too. Transportation adds another layer of expenses as finished coins need distribution across various regions. Overheads such as utilities, administrative costs, and facility upkeep also contribute significantly to the overall expense involved in producing one rupee. Each element plays its part in determining how much it truly costs to manufacture this small yet vital currency piece.
Comparison Of Manufacturing Costs Between Different Materials (E.G. Paper, Metal, Polymer)
When examining the manufacturing cost of 1 rupee coins, material choice plays a significant role. Metal coins, for instance, often involve higher production costs due to the extraction and processing of raw materials like copper and nickel. On the other hand, paper currency is generally less expensive to produce. Polymers have emerged as a modern alternative. Each material has its own lifecycle implications too.
The Impact Of Inflation On Manufacturing Costs Over Time
Inflation significantly influences the manufacturing cost of 1 rupee coins. As the economy grows, prices for raw materials and labor tend to rise. This increase can directly affect how much it costs to produce currency. For example, if metal prices surge due to market demand, the cost of minting coins also goes up. Manufacturers must adjust their budgets accordingly. Labor is another critical factor. The interplay between inflation and manufacturing highlights ongoing challenges faced by mints worldwide.
Ways To Reduce The Manufacturing Cost Of One Rupee
Reducing the manufacturing indian 1-rupee coin involves innovative strategies. Streamlining production processes is key. Automation can significantly minimize labor costs while enhancing efficiency. Sourcing raw materials locally can also lead to considerable savings. Investing in technology plays a crucial role too. Another effective approach is recycling materials used in coin production. Fostering partnerships with suppliers can result in better pricing deals for bulk purchases, ensuring that every penny counts in the manufacturing process of our currency.
Conclusion: Estimated Cost
Ek Rupee Coin Ka Manufacturing Cost Kitna Hoga?
In countries like India, it is generally observed that the cost to mint a one-rupee coin is often higher than its face value. According to reports and trends from government mints, the cost of minting a one-rupee coin can range between ₹2 to ₹3 per coin.
This discrepancy exists because governments prioritize durability, security features, and quality, ensuring the coins last longer in circulation and meet standard requirements.